Innovations in Plastic Mould Manufacture: Transforming Industries
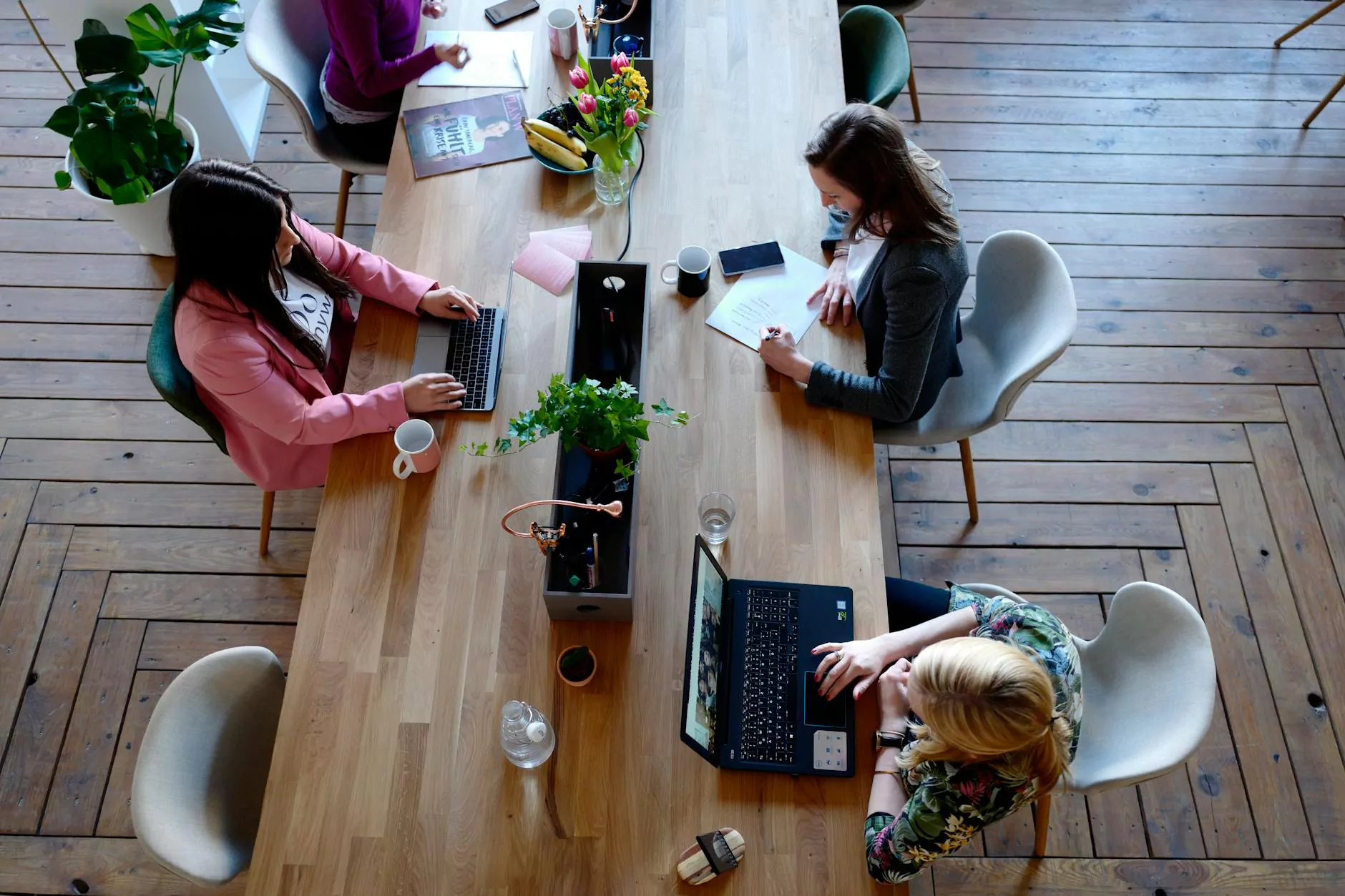
The plastic mould manufacture industry plays an integral role in the modern economic landscape. As a critical supplier across various sectors, it has evolved significantly through advancements in technology and design methodologies. This article provides an in-depth look at the processes involved in plastic mould manufacture, its benefits, and how it influences multiple industries today.
The Importance of Plastic Moulds in Modern Manufacturing
Plastic moulds are essential in producing a vast array of products that we encounter daily. From automotive components to consumer electronics and medical devices, the versatility of plastic offers several advantages:
- Lightweight: Products made from plastic are generally lighter than their metal counterparts.
- Corrosion Resistance: Plastics do not corrode like metals, extending the lifespan of products.
- Cost-effective: Plastic parts can be mass-produced at relatively low costs, making them affordable for manufacturers and consumers alike.
- Design Flexibility: Plastics can be molded into intricate shapes, allowing for innovative designs and functionality.
A Closer Look at Plastic Injection Moulding
One of the most prevalent methods of plastic mould manufacture is plastic injection moulding. This process involves injecting molten plastic into a pre-designed mould where it cools and solidifies into the desired shape. Here are the key steps involved in plastic injection moulding:
1. Design and Prototyping
The first stage involves creating a detailed design of the product and the accompanying mould. Advanced computer-aided design (CAD) software is often used, allowing for high precision and the ability to visualize the final product before production begins.
2. Mould Making
Once the design is finalized, a plastic injection mould manufacturer will build the actual mould, usually from steel or aluminum. This step is crucial as the quality of the mould directly impacts the performance and aesthetics of the final product.
3. Injection Process
During the injection phase, pre-dried plastic pellets are heated until they melt and are then injected into the mould under high pressure. This ensures that the plastic fills every cavity within the mould.
4. Cooling and Ejection
After the mould has been filled, the plastic is allowed to cool and solidify. Once set, the mould opens, and the finished part is ejected. This process can typically produce thousands of parts quickly and efficiently.
Advantages of Plastic Injection Moulding
The popularity of this method is attributed to several benefits, including:
- Efficiency: High production rates are achievable with minimal labor requirements.
- Reduced Waste: The process allows for the control of excess plastic, leading to less material waste.
- Consistency: Products manufactured through this technique are uniform and of high quality.
- Complex Designs: It enables the production of complex shapes that would be difficult or impossible to achieve through other means.
Applications of Plastic Mould Manufacture
With its versatility, plastic mould manufacture extends across numerous industries:
1. Automotive Industry
The automotive sector utilizes plastic components extensively. From interior panels to bumpers, these parts not only reduce weight but also enhance fuel efficiency and overall performance.
2. Consumer Electronics
Devices such as smartphones, game consoles, and household appliances heavily rely on plastic casing due to its insulating properties and ability to withstand heat.
3. Medical Devices
In healthcare, plastic is critical for manufacturing a wide range of medical devices such as syringes, tubing, and even surgical tools. The hygienic properties of plastic make it an excellent choice for these applications.
4. Packaging Solutions
Plastic moulds are employed in the packaging sector to create containers, bottles, and protective packaging materials, maximizing shelf life and product safety.
Understanding the Role of Plastic Mould Makers
Plastic mould makers are specialists who design and fabricate the moulds used in the injection moulding process. Their expertise in materials, design principles, and manufacturing standards ensures high-quality moulds that meet specific industry requirements. Their role includes:
- Consultation: Providing expert advice to clients on design and material selection.
- Precision Manufacturing: Utilizing advanced machining and fabrication techniques to create accurate and durable moulds.
- Quality Control: Implementing strict quality checks at every stage to ensure the moulds meet required specifications.
Challenges in Plastic Mould Manufacture
Despite its advancements, the plastic mould manufacture industry faces several challenges. Key among these:
- Cost Management: High initial costs for mould making can impact small manufacturers.
- Material Limitations: Not all plastics are suitable for high-precision applications, necessitating material research and development.
- Environmental Concerns: The industry's reliance on petroleum-based products raises sustainability issues, prompting the exploration of alternative materials.
Future Trends in Plastic Mould Manufacture
As technology continues to evolve, so too does the plastic mould manufacture industry. Here are some promising trends to watch for:
1. Automation and Industry 4.0
Automation is transforming the mould-making process, enhancing precision and reducing costs. Industry 4.0 technologies, such as IoT and big data analytics, are enabling real-time monitoring and optimization of manufacturing processes.
2. 3D Printing in Mould Production
3D printing is becoming increasingly significant in the creation of prototypes and even final production of moulds. This technology offers reduced lead times and the ability to create complex geometries with ease.
3. Sustainable Practices
With growing environmental awareness, manufacturers are adopting sustainable practices, such as using recycled materials and biodegradable plastics, to reduce their environmental footprint.
Conclusion
The field of plastic mould manufacture is continually evolving, driven by technological advancements and the increasing demand for innovative, cost-effective solutions across various industries. As we look to the future, the importance of skilled plastic injection mould manufacturers cannot be overstated; they are essential to the realization of advanced product designs and the sustainability of the manufacturing process. By understanding the intricacies of this industry, businesses can position themselves to take advantage of the numerous opportunities it presents, ensuring continued growth and success.
For more insights into the world of plastic mould manufacture, and to partner with experienced professionals, consider reaching out to Hanking Mould. With our dedication to quality and innovation, we are poised to meet your needs and help you navigate the future of manufacturing.