Understanding Plastic Injection Molding Manufacturers
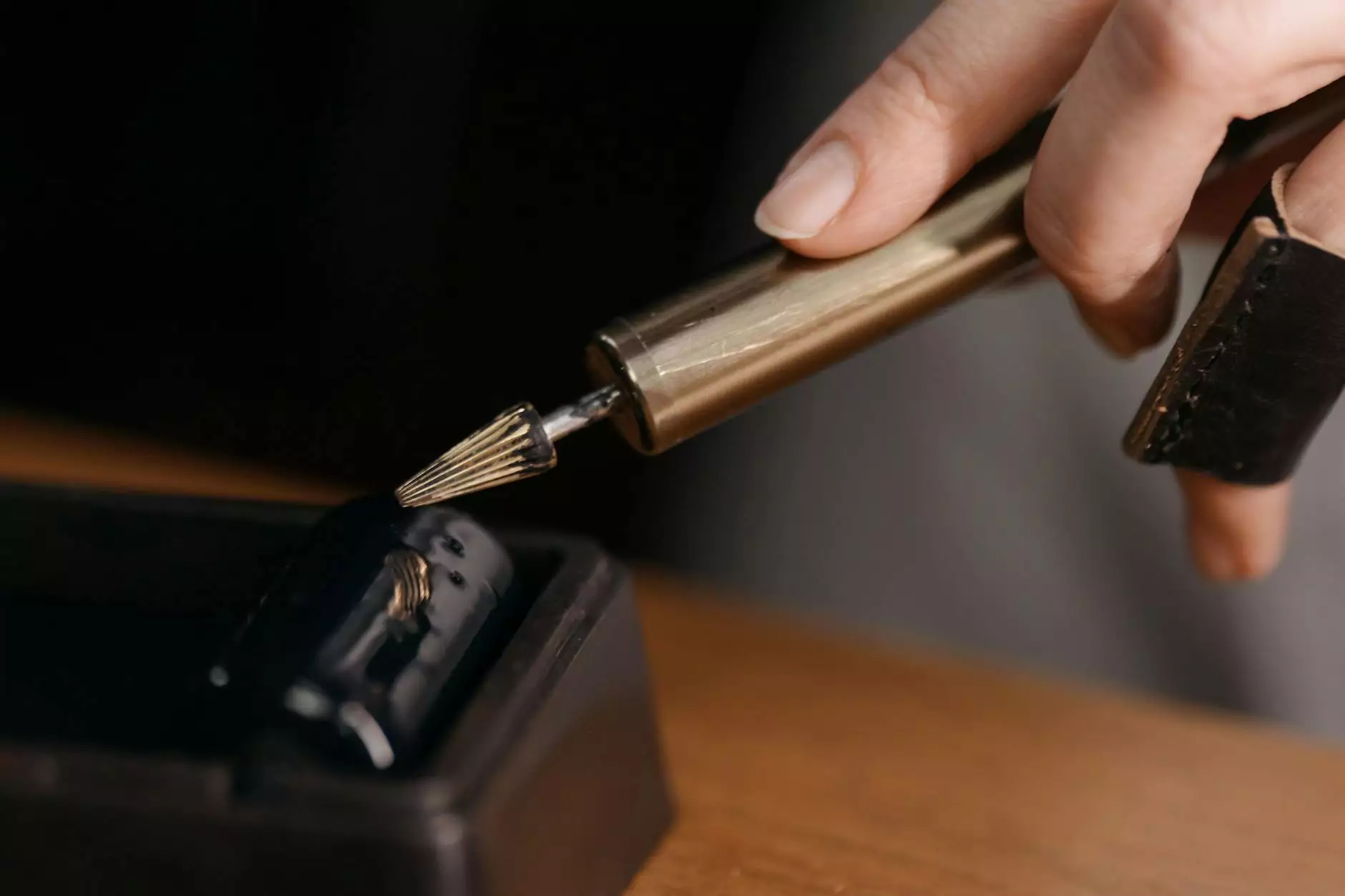
Plastic injection molding manufacturers play a pivotal role in the modern manufacturing landscape. This innovative process has revolutionized how products are designed and produced, making it an essential topic for industry professionals, business owners, and consumers alike. In this comprehensive guide, we delve into the intricacies of plastic injection molding, its advantages, applications, and the leading manufacturers worldwide, specifically highlighting the significance of companies like Deep Mould.
What is Plastic Injection Molding?
Plastic injection molding is a manufacturing process that involves injecting molten plastic into a mold to create specific shapes and designs. This technique is widely used for producing parts in various industries, including automotive, aerospace, consumer goods, and electronics. The process is characterized by its efficiency, versatility, and ability to create complex geometries.
How Does the Plastic Injection Molding Process Work?
The plastic injection molding process can be broken down into several key stages:
- Designing the Mold: The first step in the process is designing a mold that reflects the desired geometry of the end product. Engineers and mold designers collaborate to create a mold that meets specifications.
- Preparing the Material: Plastic pellets, typically made of thermoplastics, are fed into the injection molding machine, where they are heated until they melt.
- Injection: The molten plastic is injected under high pressure into the mold cavity, allowing it to fill even the most intricate shapes.
- Cooling: Once the mold is filled, the plastic is cooled to solidify. The cooling time varies depending on the type of plastic and the thickness of the molded part.
- Removing the Part: After cooling, the mold opens, and the finished part is ejected, usually with the assistance of ejector pins.
- Finishing Touches: The final step may include trimming excess material, surface treatments, or assembly of multiple components.
Advantages of Plastic Injection Molding
There are numerous advantages that drive many companies to rely on plastic injection molding manufacturers for their production needs:
- Cost-Effectiveness: Once the initial mold is created, producing each part is relatively inexpensive, making it ideal for large production runs.
- Precision and Consistency: Injection molding allows for high precision and encourages consistency across thousands of identical parts.
- Material Versatility: A wide variety of plastic materials can be used, including engineering-grade plastics that offer thermal and mechanical properties suitable for demanding applications.
- Complex Designs: Molds can be designed to create detailed features and complex geometries that are often difficult or impossible to achieve with other manufacturing methods.
- Reduced Waste: The process is inherently less wasteful than other manufacturing methods, as sprues and runners can often be reused.
Industries Benefiting from Plastic Injection Molding
Due to its adaptability, plastic injection molding serves a vast array of industries:
1. Automotive Industry
In the automotive sector, plastic injection molding is used to manufacture components such as dashboards, panels, and even intricate engine parts. This innovation leads to weight reduction and improved fuel efficiency while also lowering manufacturing costs.
2. Consumer Goods
The production of everyday items, including household appliances, toys, and packaging, heavily relies on this process. Manufacturers create aesthetically pleasing, durable, and lightweight products that cater to consumer demands.
3. Electronics
Plastic components are essential in electronics for insulation and protection. Products like mobile phones, laptop casings, and connectors often feature parts made through injection molding, enhancing their functionality and durability.
4. Medical Devices
Injection molding is also a critical process in the manufacturing of medical devices, including syringes, inhalers, and laboratory equipment. The precision and hygiene of molded parts are paramount to ensuring safety and effectiveness in medical applications.
Choosing the Right Plastic Injection Molding Manufacturer
When it comes to selecting a reliable plastic injection molding manufacturer, several factors should be taken into consideration:
1. Experience and Expertise
Look for manufacturers with a strong background and extensive experience in the industry. Their expertise will often translate into better product quality and efficiency.
2. Quality Assurance Practices
Quality should always be a top priority. Ensure that the manufacturer has rigorous quality control practices in place, including certifications such as ISO 9001.
3. Technological Capabilities
Advanced technologies such as computer-aided design (CAD) and computer-aided manufacturing (CAM) can greatly enhance the production process. A manufacturer’s investment in technology reflects their commitment to innovation and quality.
4. Customer Service and Support
Effective communication and support are crucial for a successful partnership. A manufacturer that values customer service will ensure smooth project management and prompt responses to inquiries.
5. Cost Consideration
While cost should not be the sole deciding factor, it is important to choose a manufacturer that provides excellent value for money without compromising quality.
Environmental Considerations in Plastic Injection Molding
With growing environmental concerns, the role of plastic injection molding manufacturers in sustainability is increasingly crucial. Many manufacturers are adopting eco-friendly practices:
- Using Recyclable Materials: Manufacturers are expanding their material choice to include biodegradable and recyclable plastics.
- Energy Efficiency: Many companies are investing in energy-efficient machinery to reduce their carbon footprint during production.
- Waste Reduction: Implementing strategies to minimize waste during production processes enhances sustainability efforts.
The Future of Plastic Injection Molding Manufacturing
The future of the plastic injection molding industry looks promising as technological advancements and evolving consumer needs drive innovation. Key trends include:
- Increased Automation: Robotics and AI are expected to further streamline production processes, increasing efficiency and reducing human error.
- Digital Twin Technology: This technology allows manufacturers to create virtual replicas of physical processes to optimize productivity and anticipate potential issues.
- 3D Printing Integration: The integration of 3D printing for prototyping and tooling will enhance rapid development and reduce time-to-market.
- Sustainability Initiatives: A continued focus on environmental responsibility will drive manufacturers to adopt practices that align with global sustainability goals.
Conclusion
Plastic injection molding manufacturers serve as the backbone of various industries, delivering quality, precision, and efficiency. Understanding the intricacies of this process, the advantages it offers, and its growing significance in the manufacturing ecosystem empowers businesses to make informed decisions. The move towards sustainability, coupled with technological innovation, will undoubtedly shape the future of this industry.
For businesses seeking reliable solutions in plastic injection molding, partnering with experienced manufacturers like Deep Mould ensures that quality and efficiency remain at the forefront of production processes. Embrace the future of manufacturing with the advantages offered by plastic injection molding.